+86 189 5353 7121
Operation process of bronzing machine before use 
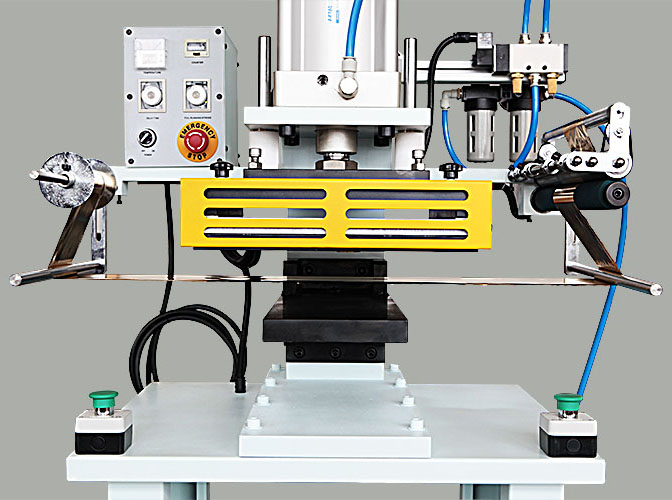
The bronzing machine mainly uses the principle of hot pressure transfer. Under combined pressure, the anodized aluminum contacts the hot-stamping plate and the substrate. Due to the heating of the electric heating plate, hot printing plate has a certain amount of heat. The heated anodic alumina melts the hot-melt stained resin layer and the adhesive, and the viscosity of the stained resin layer decreases. After melting, the viscosity of the special thermal sensitive adhesive increases, and the aluminum layer and the anodized base film are peeled off and transferred to the substrate at the same time. As the pressure is removed, the adhesive rapidly cools and cures, and the aluminum layer adheres firmly to the substrate, completing the hot stamping process.
1. There are two aspects of preparation before hot stamping: Preparation of ironing materials and hot printing plate preparation.
(1) Preparation of ironing materials: including anodizing model selection and blanking according to specifications. Different models also vary in performance and suitable materials and range for ironing, such as white paper and print with ink layer, field and dot prints, large and small sizes, etc. Therefore, the choice of anodic oxidation model should be different.
(2) hot printing plate preparation: hot printing plate is copper plate, characterized by good heat transfer performance, pressure resistance, wear resistance, no deformation. Hot stamping times, you can also use zinc plate.
2. Plate loading: stick the prepared copper plate or zinc plate firmly on the machine, adjust the rules and pressure to the appropriate position. The printing plate should be pasted and fixed on the base plate of the machine. The bottom plate is heated by an electric heating plate, and the heat is transferred to the plate for hot stamping.
3. Pad: after the plate is fixed, the pad can be adjusted for local unevenness, so that the pressure is uniform everywhere. The leveling bronzing machine should first level the embossed plate, and then paste a piece of coated paper with a weight of more than 100 g/m2 on the back of the plate material. Then touch and press the carbon paper to get the printing sample. Adjust the pressure of the plate material according to the weight of the printing sample, until the printing sample is clear and uniform.
4. Determination of hot stamping process parameters: the correct determination of process parameters is the key to obtain the ideal hot stamping effect. Hot stamping process parameters mainly include: hot stamping temperature, hot stamping pressure, hot stamping speed, the ideal hot stamping effect is the comprehensive effect of the three.
(1) Determination of temperature. The effect of hot stamping temperature on the quality of hot stamping is very obvious. If the temperature is too low, anodized insulation layer and adhesive layer melting is not sufficient, will cause hot stamping wood stamping is not complete, frosting or hot stamping is not firm. Hot stamping temperature shall not be lower than the temperature range of anodide, the lower limit of this range is to ensure the melting temperature of anodide adhesive layer.
(2) Determination of pressure. The role of pressure is to ensure that anodized aluminum can adhere to the substrate, and the hot stamping parts of anodized aluminum shear.
(3) determination of hot stamping speed. Hot stamping speed determines the contact time between anodized aluminum and the substrate, and the contact time is directly proportional to the fastness of hot stamping under certain conditions. Hot stamping speed is slightly slower, can make anodized and the base material firmly bonded, is conducive to hot stamping.